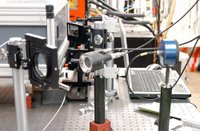
Regarding the installation of the LLG beam stabilization system at UIC it can be
stated that
1. The optimizations works properly.
2. The closed loop control works in a standard configuration i.e. beam control is achieved with a stationary 500 or 4 Hz pulse train respectively.
However, some problems encountered during the installation schedule have to be solved:
1. The motherboard of the PC delivered by LLG is defect.
The fastest solution, we suggest is that you buy a identical mainboard and replace the old one on your own. Regarding the compensation of your financial effort, we should discuss with Klaus Mann and Uwe Wachsmuth next week.
2. The contrast ratio of the pre-amplified pulses and the frontend ones are approximately one to two orders of magnitude too high. Thus, at an attenuation level sufficient to perform the closed loop control of the frontend beam,the CCD chip gets damaged after illumination with very few (app. 10) amplified pulses.
Actually the chip shows 7 damaged pixel, but this virtually does not hit the performance,as we use only a 1/16 part of the chip, so a non damaged part can be selected.
The best solution we think would be the use of a variable attenuator, based on a mechanical shutter. This shutter should have a contrast ratio of 100, and could easily be triggered by the 4Hz Trigger of the TWIN amplifier without any software support. This could be done in Goettingen, but doing it by yourself in Chicago will be much faster.
3. The closed loop control based on switching the frondend from a 4Hz to a 500Hz mode for a short time interval between two consecutive 4Hz TWIN pulses does not work. Part of this failure seems to be the high overexposure mentioned above. Another reason is probably some internal logical software bug. - However, the mode switching works, and closed loop control has been achieved without amplifier, although the software fails to set the correct values the the pulse timing schedule.
This problem should be solved in Goettingen during the next weeks. An updated version of the program may then be tested by Dr Song, who will have my full support via email or phone.
(Reported by Bernd Schaefer)