Tuesday, February 28, 2006
Changed Relay K4 and SCR on M03
Craig loaned us the used computer (400 MHz, Pentium II, better than our old one), which can be used to grab the wave froms from the oscilloscopes. I installed Tektronix WaveStar and successflully obtained the wave forms, much faster than the old machine.
Friday, February 24, 2006
Relay P40C42A12D1

The relay K4 module is P40C42A12D1-120. I found the pins were burnt due to the high current.

Thursday, February 23, 2006
Measuring the current
Tuesday, February 21, 2006
SCR CM341290
I found an interesting paper about the inverse parallel thyristor written by Dr. Henry E. Payne.
![]() Figure. 1 |
| |
![]() Figure. 2 |
http://www.payneng.com/AN11-18/AN11-18.htm
Thyristor Theory and Design Considerations(PDF)
Monday, February 20, 2006
ERATRON FPE 202 D30
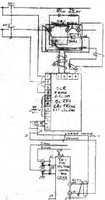
The SCR is Powerex CM341290 (Voltage 1.2 kV, Current rating: 90 A). I measured the firing angle and high voltage current.

Friday, February 17, 2006
SCR control unit
Wednesday, February 15, 2006
Keep checking C 2154 Board
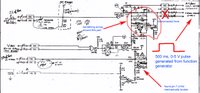
Tuesday, February 14, 2006
High Voltage Control Module R03
Friday, February 10, 2006
C-2154 PCB repaired
Thursday, February 09, 2006
Pulse Modulation Control PCB
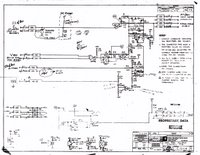
Mike helped me to check the board. We measured the pulses on pin 1 at A4, pin 7 at A4, pin 6 at A1 and pin 6 at A2. We found it's feedback to decrease the voltage of Q1 input.
Tuesday, February 07, 2006
10K Ohm resistors burned again


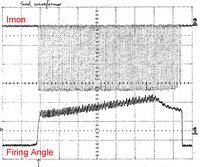
We already checked the 2155 circuit board in the box today, it's very good. We will check the 2154 board, which generate the firing angle signal.
Monday, February 06, 2006
Unltra-high Intensity Ti:Sapphire/KrF* Excimer Hybrid Laser System
1. Introduction
Based on the chirped pulse amplification (CPA) technique [1] and the Kerr-lens mode-locked Ti:sapphire laser [2], a laser intensity of 7x1020 W/cm2 has been achieved by the solid state laser system. In order to reach this intensity, a laser system with extremely high peak power of 1500 TW (440 fs, 660J at 1054nm) [3] is required, which leads the system very complicated and expensive. Since the laser intensity is inversely proportional to the square of the wavelength, the given high intensity can be reached using the ultraviolet (UV) laser with much lower peak power. The main method to produce laser pulses in the UV spectral region is using rare gas-halide excimers. Unlike in solid state laser, excimer lasers with appropriate heat exchange can avoid thermal effects such as thermal lens; also due to the less optical distortion in the gas medium, the excimer laser has an advantage to give better beam focusability. By combining compact femtosecond laser with KrF* excimer laser chain for amplification of the converted UV pulses, our old Ti:Sapphire/KrF* excimer hybrid laser system [4] is upgraded. The new system can produce the laser pulse with a peak power of 4 TW and focused intensity up to 2 x1020 W/cm2.
2. System configuration
The Ti:sapphire/KrF* laser system is composed of the front end and the large aperture KrF* excimer laser amplifier.
The front end consisted of three main parts (Fig. 1). The first part is a commercial Ti:sapphire solid-state laser system (Spectra-Physics Lasers Inc., CA), which generated a 100-fs pulse train at 745 nm with a repetition rate up to 500 Hz. The output pulse energy is around 600 mJ. The second part is using the polished BBO crystals with 0.8 mm and 0.24 mm thickness for frequency doubling and tripling respectively. A 1.1 mm thickness MgF2 wave plate is inserted between the crystals to compensate the group velocity delay after frequency doubling. The output energy from the tripler is about 120 mJ with ~100 fs at 248 nm, which is sent the third part to seed the excimer preamplifier. The excimer module is arranged in 4-pass off-axis geometry in order to reach the optimal conditions for amplifying femtosecond pulses [5]. The output from the first double-pass excimer amplifier is spatially filtered by a 150-mm-diameter pinhole in a diffraction-limited manner in the vacuum pipe. A pair of grating is placed after the first 2-pass amplifier to compensate the dispersion before propagating through the amplifier chain by adding a negative pre-chirp to the laser pulse. The output of the pre-amplifier is up to 20 mJ with ~120 fs pulse duration.
After the pre-amplification the 248 nm pulse is collimated and expanded to a 10-cm diameter beam using a 4-power reflecting telescope of Dall-Kirkham design. The final seed pulse is injected into a large aperture KrF* excimer amplifier [6]. This powerful amplifier is designed to operate at relatively low pressure and low gain in order to reduce wave-front distortion and amplified spontaneous emission (ASE). The final pulses exhibit the average energy of 600 mJ at repetition rate of 0.4 Hz. A portion of final laser pulse is sent to the frequency resolved optical gating (FROG) device for the measurements of pulse duration and phase shift. The pulse duration is ~200 fs, and the phase shift is around several mrad.
2. Focusability
In order to calculate the laser intensity at best focus, the focusability of the seed pulse after it passed through the large aperture excimer amplifier was measured. The 10-cm-diameter seed beam was sufficiently attenuated so that no air breakdown or the beam self-focusing occurred. The beam was directed onto an off-axis parabolic mirror of 20 cm focal length. The focal spot of this f/2 optical system is imaged by a 40 times UV microscope objective (Partec GmbH) onto a CCD camera (Watec-502B) without the cover window.
The beam profile at the image plane of the microscope objective is shown in Fig. 2. The focal spot size of the 248-nm seed pulse is ~1.5 mm in diameter, which is about a factor of 1.5 times larger than the diffraction-limited spot size.3. Conclusion
This upgraded system finally generates 200-fs pulse duration, the 1.5-mm-diameter focal spot size, and the laser energy of 600 mJ, which gives an average intensity of ~2?1020 W/cm2. To our knowledge, this system generates the highest laser intensity at 248 nm. We will use this laser to develop high brightness hard X-ray source from a Xe cluster target for application in biological microimaging [7].
References
[1] P. Maine, D. Strickland, P. Bado, M. Pessot, and G. Mourou, “Generation of ultrahigh peak power pulses by chirped pulse amplification,” IEEE J. Quantum Electron. QE-24, 398-403 (1988).
Friday, February 03, 2006
Systerm testing
Thursday, February 02, 2006
Changed south side thyratron CX1622
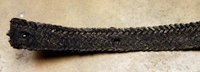

This conduct tape connected the thyratron board to the ground, that's why the sparks on the plate were always obtained. So we removed the old dirty conduct tape and put a brand new copper tape.
Because we don't have new thyratron CX1622 at hand, I installed a used one which was probably still good.
Wednesday, February 01, 2006
Keep Passivation
everything sounds very well. Now I am tracking the south side transformer primary, secondary,
filament 1st stage and 2nd stage, I hope to solve this random trigger problem soon.