Friday, April 28, 2006
The TWIN excimer laser not working
Finally we repaired the Prometheus, I tried to run the TWIN for synchronizing. However, I found the TWIN excimer did not run anymore. I changed the trigger mode to internal, there was not any output yet. I think the trigger system does not work.
Wednesday, April 26, 2006
Burks Oil Pump Overheating
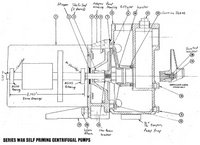
BURKS OIL PUMP OVERHAUL
TROUBLESHOOT
- Overheating motor may have burnt out winding. 3 phase amps check will show unequal values on 3 lines.
- Bad noises are probably motor bearing. Replace them immediately, or motor will be ruined.
- Oil pooling in the recess within the motor adaptor (item 5) indicates a worn shaft (ok if a new seal leaks for a very short time).
- Special tools and parts are in the closet near rm 2159.
- Standards tools: 3/8” ratchet with 9/16” + 7/16”sockets, and 12” extension. One large flat - blade screwdriver. 3/16” hex key.
- Electrical: Shut off motor switch. Label Switch, “LEAVE OFF”.
- Disconnect wiring.
- Drain: Close all oil manidold valves.
- Uncork 1/2 “Poly Flow plug at top of oil manifold, for air vent.
- Tap oil into clean beaker under pump drain valve.
- Transfer oil (If clean) to drip reservoir. Repeat until drained.
- Replace Poly Flow plug.
- Push “Pump Prop” disk (in special tools box) under pump housing.
- Unbolt pump body from motor / adaptor (bell housing): (4 bolts, item 6). Don’t loosen bolts that join motor to adaptor housing. Pull motor and adaptor housing away. Some oil will gush.
Note: No left-hand threads are used on this entire pump.
- Located rubber doughnut “Suction sleeve” (Item 12) and remove it.
- Remove “Diffuser” (cone ? shaped, item 9); just 2 small screws.
- Remove O ring (Lab unit) or paper gasket (basement unit). If paper gasket is used, meticulously clean the sealing surfaces.
- Clamp special big pinch clamp around bronze impeller, with the stud sticking through a housing hole.
- Unscrew impeller clamp bolt and brass beveled washer.Note: If screw is socket head, it has Loctite on threads. I tapped motor shaft with wrong (Course) thread, so it needs extra grip.
- Reapply Loctite when reassembling this motor.
- Pop snap cap off motor rear.
- With large screwdriver, remove impeller by “unscrewing” motor shaft.
- Catch impeller. Note flat brass washer behind impeller. Leave special pinch clamp on impeller, for reassembly.
- Remove the 4 housing bolts, and pull off housing. You are fighting the drag of the rotary seal part that grips the shaft. If it’s really stuck, use special “motor bell puller”, with the CPI nut to protect the shaft threads.
- Press stationary seal out of adaptor housing.Note rubber “slinger” washer on shaft. It needs replacing if it does not grip the shaft.
- Begin reassembly unless motor bearing need replacement.
MOTOR BEARING OUT
Motor Dismantle:
- Pull off slinger.
- Mark motor shell and ends for alignment, if not already.
- Unscrew 4 long screws from rear of motor.
- Pull front end off, with armature.
- Pull bearing: Note: It’s not necessary to remove front bearing (long shaft end), and protect shaft end from damage.
- Use shop puller to pull bearing off. Note: There may be a loose piece, a motor bearing clamp, laying loose behind bearing. Don’t forget to reinstall it.
- In like manner, remove rear bearing. Note: If damage to rear bearing is no concern, you may omit adaptor.
NEW BEARING IN
Note: Details of pressing techniques are not discussed here. One caution: Work with shaft only. Do not support or press armature body or fan.
- Clean long shaft of any rubber seal residue.Press bearing onto armature shaft short end, all the way to shoulder.
- Slip front bearing clamp (a piece of the motor), if used, onto long shaft end. Using “motor bearing installer”, press bearing onto armature shaft end, but stop when bearings measure an outside separation distance of 8.190”.
- Reassemble Motor as you took it apart. If long screws are stubborn, remove screws, sight through holes and give ends corrective rotational taps.
Note: It is reasonable to assume that a seal that has little wear and soft rubber parts should work fine if carefully dismantled, cleaned, silicone ? greased, and reassembled.
- Reinstall slinger washer, nominal 1/8” from motor face.
- Use steel wools and acetone to clean the seal recess in the adaptor housing.
- Press the stationary part of the seal into the adaptor housing, rubber lit first, using “stationary seal installer”, with the cardboard disk as a protector for the ceramic face. Even, straight, firm hand pressure is enough.
- Dab some silicone oil on the ceramic seal face.
- Grease motor shaft.
- Bolt adaptor housing onto motor.
- With the steady pressure, push spring ? loaded part of seal onto shaft, graphite first; don’t turn. Push all the way, only from the spring. As per disassembly, reinstall flat brass on shaft, then Impeller (snugly), special brass beveled washer, and shaft bolt (Loctite, only if ? - 20 threads).
- Remove impeller clamp tool.
- Replace motor rear snap cap.
- Reinstall diffuser.
- Grease and install new paper gasket or # 2- 263 O ring, as req.
- Reinstall suction sleeve on end of diffuser.
- Bolt motor adaptor to pump housing, keeping flanges evenly gapped.
- Retrieve 7/16” pump prop.
- Reconnect wiring.
- Set valves for full oil flow.
- Waite 10 minutes for oil to flood the pump.
- Remove “LEAVE OFF” label.
- Turn on pump.
Tuesday, April 25, 2006
Redrawing the system timing schematics
I combined the front end laser and the Prometheus to run. I drew the timing schematics to understand the system control easily. Then I tried to synchronize the seed laser pulse and the Prometheus. I filled new gases into the Prometheus and ran it at 20kV. This time the Prometheus was trigger by the seed laser pulse. When I adjusted the time delay between the Railgap and the X-ray anode around 1.93 microseconds, I measured the maximum UV light. However, I could not synchronize the seed beam with the Prometheus very well. Another problem is the oil recycling system, the oil pump could notbe run, the light show it's overheat.
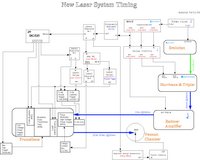
Eurotherm Firing Angle Control for Prometheus Operation
1. Introduction
Recently UIC purchased a Eurotherm 7100A SCR Controller to replace the no longer supported Eratron FPE 202-D30 SCR Controller. This Technical Note will discuss ways in which to utilize not only the Euroterm Controller but also any generic SCR controller for the charging of the main Thyratron Capacitor Banks. One goal of changing to a commercial controller is to eliminate much of the troublesome Firing Angle and PC Board Control cards that were utilized for the Eratron unit. The Eurotherm unit as ordered is a basic unit without “alarms” or “soft start” features that are useful in driving inductive loads like the HV Transformer. More advanced units incorporate a “safety ramp” that involves progressively increasing the Thyristor firing angle in order to apply the voltage (and current) to the load smoothly and thus reduce the start-up current of loads which either have a low resistance when cold or are inductive. For inductive loads, the “safety ramp” prepares the initial magnetization of the transformer to avoid saturating transformers on power up that can lead to large in rush currents to the primary. This note will show via simulations that it is relatively straightforward to control the present Eurotherm unit and incorporate “soft start” features.
2. Circuit Model Description
This circuit is essentially the same as that shown in the note “Firing Angle Control of SCRs during Charging”, 26 March 2006. The main addition to that circuit is the generation of the SCR control voltages (E1 and E2) by the Eurotherm unit, which is driven by a 0 to 5 Volt DC control signal. V1 is the 208 VAC rms line voltage and the “ideal” HV transformer has been modeled as having a 32kVAC rms output voltage (turns ratio of 154) with a secondary resistance, R5, of 2K ohms. R1 is the 0.1-ohm peak inrush current limiting resistor to protect the SCRs. The diodes are made up of three SCH20000 diodes in series and labeled as D1 thru D4. R3 is the series-charging resistor of 100K made up of ten; 10K 225-watt wire wound power resistors. The North and South capacitor banks are labeled as C1 and C2 and interconnected with a 3K resistor. R2 is the 70-ohm resistor for purposes of monitoring the pulsed charging current (Imon). The actual Pulse Modulator (PM) HV Schematic of Prometheus (see D-2151) shows a Transzorb 5KP6.0A that clips the Imon signal at a voltage ranging from 6.67 to 7.37 volts. This is done in order to accommodate the Pulse Integrator of the PM HV Control Board (see C-2154). This is not necessary for use of the Eurotherm unit and no feedback current via Imon is needed.
3. Results of Simulations
In the event of the SCRs becoming shorted or commanded to full on, the resistor charging string is the only limit to the charging current pulses and the time that it takes for the system to reach a full voltage of 32kVAC rms x 1.414 = 45 kVDC. The purpose of the PM Voltage Control Timing Circuit (see C-2155) is to limit the charging time available with the SCRs commanded to full on such that the Thyratron Bank Voltage as indicated by Emon never exceeds 30kV although the Anode rating of the CX1622 Thyratrons is 35kVDC. This time should include the “soft start” feature of about 8 full SCR firing cycles or 0.133 seconds. The results of a simulation showing the SCR Firing Angle (set at 180 deg), the Imon current pulses, the Emon charging voltage, and the first 0.2 seconds of the Transformer Primary Voltage, gives a maximum desired charge time of 0.820 seconds. The Top trace (Red) shows the Firing Angle ramping up to 180 degrees in 0.133 seconds with the corresponding Transformer Primary Voltage being given a “soft start” over 8 full cycles as shown in the Bottom trace (Black). The Imon current pulses are shown in the 2nd trace (Magenta) and charging resistor limited to 420ma with the Emon voltage of the 3rd trace (Blue) indicated at the complete charge of 30kV in 0.82 seconds.
If the SCRs or the Controller fails such that the SCRs stay on, then the only protection to stopping the charging cycle of the capacitor banks is to command open the AC Contactors that drive the input to the HV transformer. This means that if the Emon voltage continues to increase after 0.82 seconds, the contactors must open before 1.25 seconds, which is the time that the system will reach 35kVDC on the Anodes of the Thyratrons. Some sort of comparator circuitry for Vref and Emon would appear to be needed to actuate the opening of these HV transformer contactors. Although a version of this circuitry exists on schematic C-2154, there are simpler ways to implement this fault protection. One way that is already being used is that the Thyratron banks are being fired just after the time when the charge is complete.
Although it might seem complex to generate a ramp for the firing angle control, a simple pulsed RC circuit (time constant about 0.2 seconds) driven by the present Output Transistor of the PM Voltage Control Timing Circuit (see C-2155) could be utilized. The results are shown on the bottom four plots on the next page and can be compared to those at the top of the page for the linear ramp of the “soft start”. Note that any additional complexity in ramping the top of the firing angle voltage is not necessary since ALL SCRs and Diodes are being operated safely within their limits.
(Written by Randy)
Recently UIC purchased a Eurotherm 7100A SCR Controller to replace the no longer supported Eratron FPE 202-D30 SCR Controller. This Technical Note will discuss ways in which to utilize not only the Euroterm Controller but also any generic SCR controller for the charging of the main Thyratron Capacitor Banks. One goal of changing to a commercial controller is to eliminate much of the troublesome Firing Angle and PC Board Control cards that were utilized for the Eratron unit. The Eurotherm unit as ordered is a basic unit without “alarms” or “soft start” features that are useful in driving inductive loads like the HV Transformer. More advanced units incorporate a “safety ramp” that involves progressively increasing the Thyristor firing angle in order to apply the voltage (and current) to the load smoothly and thus reduce the start-up current of loads which either have a low resistance when cold or are inductive. For inductive loads, the “safety ramp” prepares the initial magnetization of the transformer to avoid saturating transformers on power up that can lead to large in rush currents to the primary. This note will show via simulations that it is relatively straightforward to control the present Eurotherm unit and incorporate “soft start” features.
2. Circuit Model Description
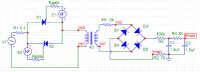
3. Results of Simulations
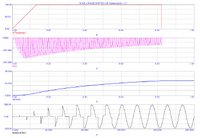
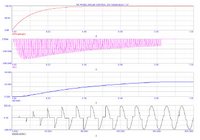
Although it might seem complex to generate a ramp for the firing angle control, a simple pulsed RC circuit (time constant about 0.2 seconds) driven by the present Output Transistor of the PM Voltage Control Timing Circuit (see C-2155) could be utilized. The results are shown on the bottom four plots on the next page and can be compared to those at the top of the page for the linear ramp of the “soft start”. Note that any additional complexity in ramping the top of the firing angle voltage is not necessary since ALL SCRs and Diodes are being operated safely within their limits.
(Written by Randy)
Monday, April 24, 2006
Clipped Imon Signals
Randy sent an email talking about the I_mon Clipped signals.
=======================
=======================
I looked more carefully at the Schematic D-2151 and just noticed that the Transzorb is actually a 5KP6.0A which has a breakdown voltage between 6.67 and 7.37. The scope traces that you sent show the Imon peaks clipping at about 6.7 volts and so this all makes sense now. This explains to me why the current peaks have always looked near constant in amplitude and yet the Emon voltage charges exponentially. The "true" Imon pulses are probably decaying exponentially in time as I have calculated in previous models. This also means that the circuitry of schematic C-2154 is not driven by what the Imon current is really doing; the Imon pulses are acting more like an "enabling" gate. This circuit is not as smart with Imon feedback as I had thought but nevertheless I still need to understand what it does in more detail.
In summary, I am looking at this circuit (C-2154) more carefully to understand what it really does. I will also model and make some comments on what the Eurotherm Controller should do for a DC command input and how the system should charge versus various but constant phase angles (this is very simple to implement). In my mind, the ideal Firing Angle input should have a "soft start" ramp for about 8 AC cycles followed by an "average" Phase Angle that has an upward ramp to somewhat increase the area of the charging pulses and therefore enable the Thyratron Capacitor Bank to charge more near linear versus exponential. Although this process can be more efficient and quicker in time, the actual charging of the banks is of little consequence as long as no SCR or Diode ratings are exceeded. The ratings are safely limited by the 100k resistor charging string other than for the initial turn on that is governed by the magnetizing current of the transformer core.
Randy
Randy
Friday, April 21, 2006
Computer control SDG II
The SDG II can be controlled with a standard RS-232 serial port. I made a standard 9-pin D-sub male/female extension cable for hookup. Only three pins are used for serial communications:
Through the serial communication, I can control the Hurricane laser repetition rate acuurately. By sending command "set:rate 0127", the rate was fixed at 507Hz/127=3.99Hz.
Pin | Function |
2 | SDG II trnsmit data, computer receive data |
3 | SDG receive data, computer transmit data |
5 | Gound |
Through the serial communication, I can control the Hurricane laser repetition rate acuurately. By sending command "set:rate 0127", the rate was fixed at 507Hz/127=3.99Hz.
Thursday, April 20, 2006
Synchronizing the seed pulse
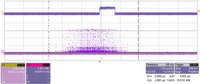
Tuesday, April 18, 2006
Timing for whole system
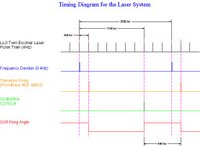
Monday, April 17, 2006
Moving the time delay forward

There were no miss fire when I set the delay time less than 1480 ms when I increased the high voltage up to 20 kV. After I fix the Prometheus timing, I will try to send the seed beam and adjust the time to synchronize them.
Friday, April 14, 2006
Calibrating the charging voltage
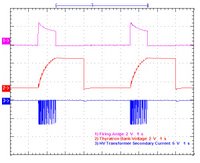
During these measurement, it was noticed that erratic charging occured at the higher voltages above 15kV and, in fact, the sytem operated correctly only every other pulse. The pulse rate was then slowed down to one pulse every 5 seconds. Although the initial timing adjustment seemed logical and worked up to 15kV, further insight from the above trace indicated that it is desirable that there be a longer recovery period after thyratron firing before commanding the system to charge. The Thyratron should recover very rapidly (less than 1ms)but the induced transient noise in the system may need a much longer recovery period in order for the present firing angle electronics to work properly. This can be seen in the slight negative signal right after Thyratron firing and to last about 0.2 seconds. Rather than increasing the Charging Delay to about 2.5 seconds as had been done, the delay should have been reduced to about 0.8 seconds. This would have resulted in a charging delay of 0.8 seconds, a charge time of 0.9 seconds, and a charge hold time of 0.8 seconds for a total cycle time of 2.5 seconds. As mentioned previously, the system was finally run at 0.4Hz at 15kV for about one hour with no adverse heating of the charging resistors being noticed. Although the evidence presented somewhat confirms that timing has been the main problem during the past 4 months, only operation at higher voltages and longer periods of time can guarantee that the charging resistor problem is “really” fixed. (from Randy's report)
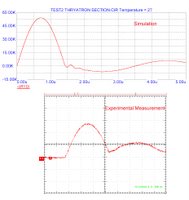
DIAL | H.V. Probe(kV) | Control Panel Meter (kV) | C-2153 J1 (V) |
6.16 | 11.10 | 14.0 | 3.35 |
7.10 | 13.00 | 16.5 | 3.91 |
8.72 | 15.25 | 19.6 | 4.6 |
10.00 | 19.00 | 24.5 | 5.7 |
Thursday, April 13, 2006
Adjusting the time delay 2498 ms

The scope traces are shown below. The lower trace shows that the charging current pulses are nearly constant in amplitude. This does not lead to constant power charging of the capacitors as evidenced by the exponential rise of the voltage in the middle trace. This exponential rise is further aggravated by the fact that the firing angle of the top trace is decaying in time whereas it should be probably be increasing in time.
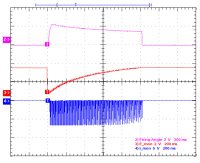
Wednesday, April 12, 2006
Invesigating the main charging system
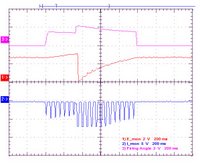

Tuesday, April 11, 2006
Removing ERATRON from X-ray Anode control system

In the beginning, we could not drive the Hiptronics to 30 kV, the output was only 15 kV. However, the output could reach 30 kV when we energized it with regular 120 VAC power. So we tried to exchange 208 VAC phases, the Hiptronics ran normally after phase exchanging. I could detect the x-ray flux.
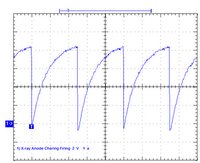
Randy measured the Primary resistance of H.V. transformer by measuring the current of a DC voltage around the transformer. The value is about 30 miliOhm. Unfortunately we were not successful in measuring the inductance with General Radio Bridge.
Monday, April 10, 2006
Installing the New Grounding System


Friday, April 07, 2006
Time of Flight Mass Spectrometer
Subscribe to:
Posts (Atom)